Partnership
Kiefel Technologies
We are proud to partner with Kiefel Technologies to bring Molded Fiber research and development to 蜜桃社区. Our new NATUREFORMER KFT LAB allows us to use the fiber of your choice to make molded fiber parts. Use any of our three in-house molds, bring your own, or work with Kiefel for your desired shape. The possibilities are endless.
Rethinking product design
We put your product first鈥攔ethinking product design, functionality, material, and composition towards a more sustainable product. Upon completion of product analysis, Kiefel and 蜜桃社区 can adapt and optimize the manufacturing process and tools to forge a production plan. The result is an easily recycled, sustainable product. Partnering together, we will close the loop.
Technical packaging:
- Agriculture or gardening needs e.g. flower pots, planting trays, cultivation systems
- High-quality technology packaging e.g. smartphones
- Product and transport protection
- Pharmaceutical disposable products
FOOD:
- Beverage cups
- Candy or cookie wrappers
- Salad bowls, fruit bowls
- Pasta cups
- Ready-to-eat/take-away containers
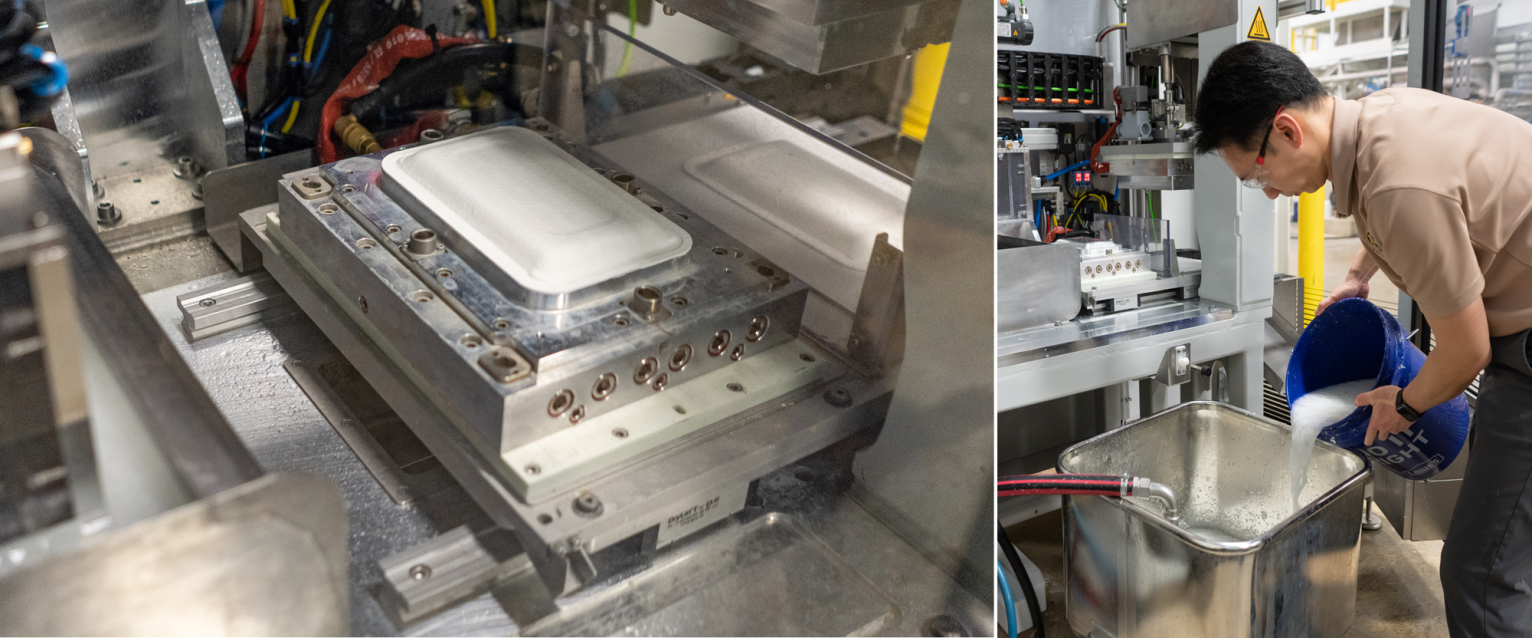
Benefits of fiber-based packaging
Benefits
- Sustainable packaging solutions
- Shock absorbing, resistant, volume reducing
- Biodegradable, reuse of waste paper or use of renewable raw materials, low CO2 footprint.
- Made from renewable materials
- Recyclable in paper recovery streams
- Grease and water-repellent products by coating or material composition, surface finishing with ink & printing.
- Customized shapes/product design
Materials for processing are common fibers of paper production (primary or secondary fibers).
Materials for processing e.g.:
- CTMP (chemi-thermical mechanical pulp)
- NBSK (northern bleached softwood kraft)
- UKP (unbleached kraft pulp)
- ONP (old newsprint)
- OCC (old corrugated containers)
- Non woods such as hemp and bagasse
Kiefel KFT Lab V03 Wet Molded Fiber Machine
Raw material: primary or secondary fibers
Fiber preparation: chemical cooks, refining and chemical addition
Forming: the majority of the water is extracted from the fiber mixture through the forming tool via negative pressure
Pre-pressing: continuous extraction of water, preformed product is pre-pressed and further drained with elastic tool
Hot-Pressing: reduction of residual moisture to a minimum through pressure and heat, refinement of contours/engravings, handover to lifting conveyors
- Stock preparation
- Vacuum unit
- Suction tool
- Control cabinet
- Pre-pressing station
- Headbox
- Hot press station
- Control panel
- Pulp basin
- Product pusher
- Product unloading
- Grey water/vacuum vessel
Contact us with your research and development needs.